Optimizing the shape of shoe soles
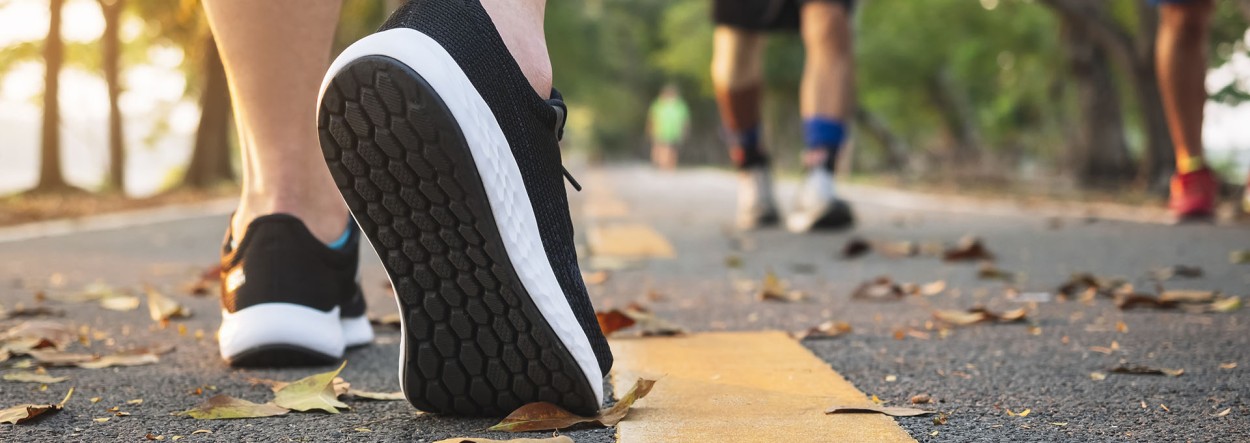
During a run, the impact of the foot with the ground produces a shock that causes vibrations to travel down the legs. To improve the comfort of athletes, companies that design sports shoes are innovating in the design of soles that dampen vibrations.
In the framework of the Chair "Design and Modeling of Innovative Materials" of École Polytechnique, supported by Arkema, Antoni Joubert, PhD student at the Solid Mechanics Laboratory (LMS)*, worked on optimizing the shape of shoe soles. His objective was to determine the optimal shape to dampen vibrations as quickly as possible after impact. This is a modeling work, in collaboration with the Center for Applied Mathematics (CMAP)**.
To develop his program, the researcher worked gradually, increasing in complexity: first from a one-dimensional (1D) beam model, then from a two-dimensional (2D) plate model, before adding a certain thickness to move on to three dimensions (3D). Finally, he used a 3D model of a real sports shoe sole.
He numerically simulated a vibration wave to which the sole would be subjected, and observed the reduction of its amplitude by the polymer material that constitutes it. This one was chosen for its viscoelastic properties, i.e. its double faculty to dissipate the energy (viscosity) like that transmitted during a shock, and to find its initial shape after a deformation (elasticity).
Starting from an initial sole drilled at several locations, he sought the optimal shape of the holes that would maximize the speed at which the vibration wave is attenuated. These calculations were performed while maintaining an equal amount of material and a certain stiffness regardless of the shape of the footing, important parameters for industrial problems.
The optimal shape for the tested material presents a 17% higher damping gain than the initial sole, a real improvement! Its appearance can be surprising: the optimized sole has both holes opening on the outside and forming galleries, and hollow places inside its thickness (more details at the end of the article).
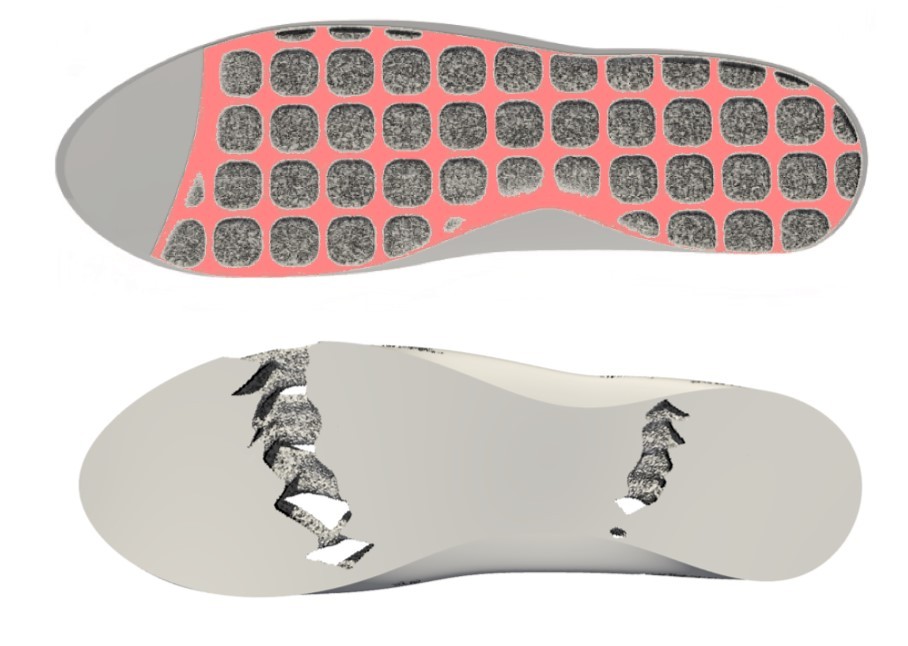
This image shows a cross-sectional view of the original (pre-optimization) footing and a view from below the optimized footing. The white areas show the holes on both sides of the sole. Image provided by Antoni Joubert.
Antoni Joubert successfully defended his thesis on December 15, 2022, entitled "Optimization of viscoelastic structure shapes under dynamic loads". This is the first doctoral thesis defended within the framework of the "Design and Modeling of Innovative Materials" Chair at École Polytechnique. This multidisciplinary work was directed by Julie Diani, researcher at the LMS and also holder of the Chair, as well as by Grégoire Allaire and Samuel Amstutz, both professors at CMAP.
When asked about the specificity of doing his doctoral thesis within the framework of a Chair, Antoni Joubert emphasized the advantage of working on an applied research topic, while maintaining his academic freedom. During his thesis, he also had the opportunity to spend two weeks a year at Arkema to talk with their Research and Development (R&D) team.
"Until then, I had mainly worked in academic research laboratories. I appreciated the opportunity to see how a corporate R&D team works, and to share knowledge with the team there," he explains.
"Arkema's support for this work reflects the importance of modeling for the development of high-performance, environmentally friendly specialty materials," said Nessim Ghamri, Head of R&D at the Rhône-Alpes Research Center. "Thanks to the models that have been developed, Arkema will be able to optimize the mechanical behaviour of polymeric materials, composites and adhesives, by studying the links between microstructure and mechanical behaviour for various applications (sports, new mobility, renewable energy)."
For the future, Antoni Joubert as a new doctor wishes to pursue numerical simulation, and is considering to move towards industry.
*LMS: a joint research unit CNRS, École Polytechnique, Institut Polytechnique de Paris, 91120 Palaiseau, France
**CMAP: a joint research unit CNRS, Inria, École Polytechnique, Institut Polytechnique de Paris, 91120 Palaiseau, France
To go further...
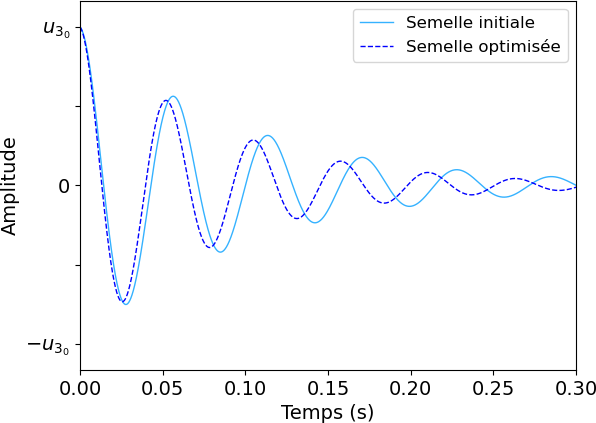
These curves represent the damping of the vibration wave by the initial sole model (solid line), and by the one whose shape has been optimized (dotted line). We can see that in both cases, the amplitude of the wave reduces over time, and this happens faster with the optimized sole which is more efficient at damping the vibration. Image provided by Antoni Joubert.
The surprising shape of the optimized sole is explained by the stiffness condition imposed during the optimization. This condition is derived from a classical bending test used in the industry to test the fatigue of the soles. One of the perspectives of the thesis work recommends to replace this bending constraint by a loading condition representative of walking or running.
This work, initially focused on the improvement of damping, can be directly extended to the improvement of the dynamism (property somehow opposite to damping) of the shoe sole for sport applications such as running.
About the Arkema Chair « Design and modeling of innovative materials »
Since its creation in 2018, the "Design and Modeling of Innovative Materials" Chair has sought to invent the materials of tomorrow with a particular interest in optimizing their mechanical behaviorr. Led by Julie Diani of the Solid Mechanics Laboratory (LMS), in collaboration with the Center for Applied Mathematics (CMAP) and with the support of Arkema, the research of this Chair focuses on the link between microstructure and mechanical behaviour of polymers and on the optimization of the behaviour of polymer structures for various applications such as adhesion, dynamic behaviour...